Production Process - Mold Core
The mold core is made using 45# steel. Both sides of the mold core are milled using a side milling machine, with a grinding amount that ranges from 0.8-1mm. The lift holes are then drilled into the 4 sides of the mold core, and a gantry milling machine is used for milling both faces. The faces themselves undergo a rough grinding through the use of a grinding machine, and each of the four sides on the mold core are made using a TIG welding process. Grinding ensures all faces and sides are accurately ground into the correct, finished sizes. The next step adds R-edges and pry slots using high speed milling, followed by a sand blasting treatment on the concave surface of the mold core. A single die is combined with the mold core using a mold gel, then after a period of vulcanization, the four mold sides are polished. Finally, pack and store the machine for delivery.
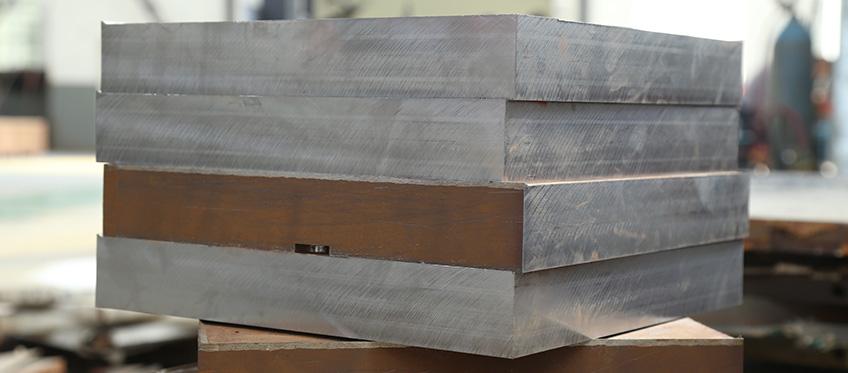
Production Process - Mold Assembly
The mold assembly is comprised of the frame, bottom plate, push top plate, magnetic base and other components. The faces and sides of all incoming material are milled using a milling machine, with the drilling machine used for material layout. Rough grinding on faces is carried out using the grinding machine, and the inner chamber is accurately milled to the required finish size with the use of a milling machine, and the hole, by a drilling machine, according to technical drawings. Finally, assembly line employees assemble the inner chamber with the alloy side panel according to the predetermined parameters. The six faces of the magnetic base are milled, and the holes drilled, allowing electricians to insert the magnetic coils. All components are then fully assembled according to the parameters. After inspection, the mold assembly is packed and stored, or delivered.
Tour Our Facilities
Gantry Milling Machine in Processing
Gantry Grinding Machine in Processing
Sintering process with hot pressing